How Does SLS (Selective Laser Sintering) 3D Printing Work?
Selective Laser Sintering (SLS) 3D printing is one of the most advanced methods in additive manufacturing, widely used in industries such as aerospace, automotive, and healthcare. SLS creates parts by using a high-powered laser to selectively fuse small particles of powder into solid structures. This technology is renowned for producing durable, functional parts with complex geometries that would be difficult or impossible to achieve with traditional manufacturing methods. The key to its success is the ability to print strong, high-resolution parts without the need for support structures.
In this article, we’ll explore how SLS 3D printing works, the essential components of an SLS printer, its advantages and limitations, and common applications in various industries.
How SLS 3D Printing Works
SLS 3D printing relies on a process called sintering, which uses heat to fuse powdered material, typically nylon or other thermoplastics. Here’s a step-by-step breakdown of the process:
Preparation of the 3D Model: As with all 3D printing methods, the process starts with a digital 3D model created using CAD (Computer-Aided Design) software. This model is then sliced into thin layers using specialized software, which generates the instructions for the printer.
Powder Bed: The printer contains a bed of fine powdered material, usually a thermoplastic like nylon. The powder is spread across the build area in a thin, even layer by a recoater blade.
Laser Sintering: A high-powered laser (usually a CO2 laser) is directed at specific areas of the powder bed. The laser selectively heats the powder particles to just below their melting point, causing them to fuse together. This process is repeated for each layer, with the unfused powder acting as a natural support structure for the layers above it.
Layer-by-Layer Construction: After each layer is sintered, the build platform lowers slightly, and a new layer of powder is spread over the previous one. The laser continues to trace and sinter the object layer by layer until the entire part is complete.
Cooling and Post-Processing: Once printing is complete, the printed part is allowed to cool within the powder bed. The surrounding unsintered powder is then removed, often with the help of compressed air or other tools. The part may also require additional post-processing, such as surface smoothing, dyeing, or additional finishing.
This process makes SLS ideal for creating parts with complex geometries, as there is no need for support structures, which are often required in other 3D printing methods like FDM or SLA.
Key Components of an SLS 3D Printer
SLS 3D printers are highly specialized machines, consisting of several key components that enable the precise sintering of powdered material:
Laser: A high-powered CO2 laser is used to selectively sinter the powdered material. The laser is controlled by the printer’s software and moves across the X and Y axes to trace the outline of each layer.
Powder Bed: The powder bed is where the material is spread and sintered. It consists of a reservoir of powdered material that is evenly distributed across the build area by a recoater blade.
Recoater Blade: The recoater blade plays a crucial role in ensuring that each new layer of powder is spread smoothly and evenly over the build platform, maintaining a consistent layer thickness.
Build Platform: The build platform lowers incrementally as each new layer of powder is sintered, allowing the part to grow layer by layer within the powder bed.
Powder Removal System: After printing, the unfused powder must be removed from around the finished part. This system typically uses air filtration or vacuum systems to recover and recycle the excess powder for future use.
Each of these components works in harmony to ensure that the SLS process produces strong, accurate parts with a high level of detail.
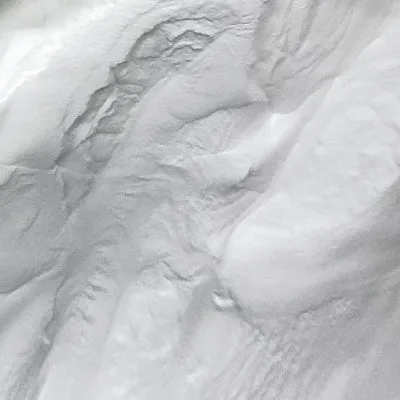
Advantages and Limitations of SLS 3D Printing
Advantages:
No Need for Support Structures: Unlike FDM or SLA, SLS does not require support structures because the surrounding powder naturally supports the part during printing. This allows for the creation of complex geometries and interlocking parts.
Strong, Functional Parts: SLS produces parts with excellent mechanical properties. The materials used, such as nylon, are strong and durable, making the prints suitable for functional prototypes and end-use applications.
Wide Range of Materials: SLS can print with a variety of materials, including nylon, glass-filled nylon, and thermoplastic elastomers, allowing for flexibility in material properties and applications.
High Productivity: Since multiple parts can be printed simultaneously in the powder bed, SLS is a highly efficient process for batch production.
Limitations:
Expensive Equipment: SLS 3D printers and the associated materials are significantly more expensive compared to FDM or SLA technologies, making it less accessible to hobbyists and small businesses.
Rough Surface Finish: While SLS parts are mechanically strong, they often have a rough surface finish that may require additional post-processing, such as polishing or sanding.
Post-Processing: Removing the excess powder can be a time-consuming process, and additional steps like surface smoothing or dyeing are often required for aesthetic or functional purposes.
Limited Color Options: SLS primarily prints in white or grey nylon, with color customization often requiring additional dyeing processes.
Common Applications of SLS 3D Printing
SLS is a highly versatile and robust 3D printing method, making it ideal for various industries:
Aerospace and Automotive: The ability to print durable, lightweight parts with complex geometries makes SLS popular in the aerospace and automotive industries. It is used for creating functional prototypes, custom tools, and even end-use parts in these fields.
Medical Devices: SLS is used to produce custom medical devices, implants, and prosthetics. The biocompatibility of certain SLS materials makes them suitable for creating patient-specific parts.
Consumer Goods: From footwear to eyewear, SLS is utilized in the production of custom consumer goods. Its ability to create complex, durable parts makes it ideal for low-volume manufacturing and prototyping.
Manufacturing Aids: Many manufacturers use SLS to produce jigs, fixtures, and tooling that improve production efficiency. The strength and durability of SLS-printed parts allow them to withstand the rigors of the factory floor.
Research and Development: SLS is often used by research and development teams to create prototypes that require high strength and durability. Its ability to print functional parts quickly makes it a valuable tool for iterative testing and development.
Conclusion
SLS 3D printing is a powerful and versatile manufacturing process that excels in creating durable, functional parts with complex geometries. By using a high-powered laser to sinter powdered materials, SLS eliminates the need for support structures and enables the production of intricate designs that are both strong and precise. Although the technology comes with higher costs and some post-processing requirements, its advantages—such as mechanical strength, material versatility, and scalability—make it a preferred choice for industries ranging from aerospace to medical devices. As SLS technology continues to advance, it will likely play an even greater role in the future of manufacturing and innovation.